In most climate zones, conditioned unvented crawlspaces perform better than vented crawlspaces in terms of safety, health, comfort, durability, and energy consumption. Research has demonstrated that these conditioned crawlspaces also do not cost more than vented crawlspaces. Crawlspace venting is a widely accepted business practice across the country. However, in humid climates, the warm, moist air entering the crawlspace is more likely to condense on crawlspace framing than to help dry out the crawlspace. This is because the outside air often has a dew point higher than the interior crawlspace framing surface temperature. As evidence, existing vented crawlspaces have experienced severe moisture and mold problems costing builders and homeowners significant resources to repair.
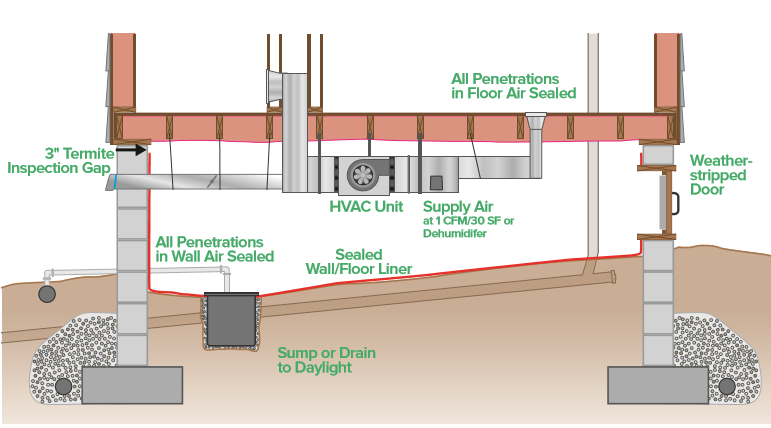
Unvented Crawlspace
The housing industry has been reluctant to use unvented crawlspaces despite their compelling benefits and the history of problems with existing vented crawlspaces. One of the reasons commonly cited by builders and designers is “the code does not allow me to build unvented crawlspaces.” This is both generally correct and misleading. The model codes do not allow the construction of “unvented” crawlspaces—except in minimal circumstances, but they do allow the construction of “conditioned” crawlspaces. The distinction is important and necessary.
Unvented, conditioned crawlspaces with insulation on the perimeter perform better in terms of safety and health (pest control), comfort (warm floors, uniform temperatures), durability (moisture), and energy consumption than passively vented crawlspaces with sub-floor insulation. This is because they are calmer and dryer in the summer, which minimizes condensation on framing surfaces. In addition, there is less heat loss from home during winter, which results in more comfortable floors and less risk of freezing pipes. Crawlspace temperatures, dew points, and relative humidities should mirror the house interior.
Crawlspaces should be designed and constructed as mini-basements, as part of the house within the conditioned space. To meet code requirements, the crawlspace floor should:
- be covered with a ground cover consisting of 6-millimeter plastic that is overlapped and sealed at the edges and secured to the side walls;
- perimeter walls should be insulated to code-specified levels (e.g., rigid foam on the exterior or inflexible fiberglass, spray foam, or rigid foam on the interior); and
- Perimeter drainage should be provided just like a basement when the crawlspace ground level is below the ground level of the surrounding grade.
The crawlspace can be conditioned in one of three ways:
- supply air from the home to the crawlspace,
- return air to home via transfer grille or to outside via exhaust fan, or
- connect the crawlspace to a conditioned basement.
A soil gas venting system should be installed as part of a complete radon-resistant construction system.
Research encourages using slab-on-grade foundations rather than crawlspaces for locations not subject to frequent flooding.