A home inspection is a crucial step in the real estate process in California. But who attends a home inspection in California? Knowing the key players and their roles can help buyers and sellers navigate this essential phase confidently. This detailed guide will explore who typically attends, their responsibilities, and why their presence is necessary.
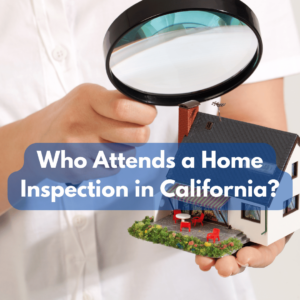
Who attends a home inspection in California?
Key Attendees at a Home Inspection in California
The Home Inspector
The home inspector is the most critical attendee at a home inspection in California. These certified professionals are responsible for thoroughly examining the property and identifying potential issues or defects that could impact the home’s value or safety. During the inspection, they will assess the structural integrity, electrical systems, plumbing, roofing, and more.
Why It Matters: The home inspector’s detailed report provides a comprehensive overview of the property’s condition, helping buyers make informed decisions and sellers address any issues beforehand.
The Buyer
The buyer should always attend the home inspection. Being present allows buyers to understand better the property they are purchasing. It’s an invaluable opportunity to ask questions and learn about the home’s current state and any future maintenance it may require.
Why It Matters: Buyers can directly interact with the inspector, gain insights into potential concerns, and learn how to maintain their new home effectively.
The Buyer’s Agent
A buyer’s real estate agent is supportive during the home inspection. Their presence is crucial as they can help interpret the findings and advise how to proceed. Whether negotiating repairs or adjusting the offer based on the inspection report, the agent’s expertise is vital.
Why It Matters: Agents ensure buyers fully understand the implications of the inspection results and provide guidance on the following steps to protect their interests.
The Seller
While not always required, the seller may attend the home inspection. Their presence can be beneficial if there are specific questions about the property’s history or any recent repairs. However, it’s often recommended that sellers give the inspector and buyer space to inspect without feeling pressured.
Why It Matters: Sellers can provide immediate answers to any queries and gain firsthand feedback from the inspection, which can help make necessary repairs before the sale.
Other Potential Attendees
Specialists or Contractors
Sometimes, specific issues like mold, foundation problems, or HVAC concerns might require the expertise of a specialist. Having these professionals on-site during the inspection can provide detailed assessments and estimates for repairs.
Why It Matters: During the inspection, specialists can better understand significant issues, allowing for more accurate cost evaluations and repair plans.
Family Members or Friends
Buyers might bring trusted friends or family members along for a second opinion or emotional support. This can be especially helpful for first-time homebuyers who might feel overwhelmed by the process.
Why It Matters: Extra eyes and ears can help ensure that all aspects of the inspection are understood and any concerns are thoroughly addressed.
Why Knowing Who Attends a Home Inspection in California Matters
Understanding who attends a home inspection in California is essential for several reasons:
- Clear Communication: Having the right people present ensures that any questions or concerns can be immediately addressed, leading to better communication between all parties involved.
- Informed Decisions: For buyers, being present at the inspection provides a clearer picture of the property’s condition, allowing for more informed purchasing decisions. Sellers benefit from understanding potential issues needing attention before finalizing the sale.
- Negotiation Power: The inspection report can significantly impact negotiations. Knowing the property’s condition effectively helps buyers and sellers negotiate repairs, price adjustments, or other terms.
- Smooth Transactions: A well-attended inspection helps prevent surprises later in the process. It ensures that everyone has a shared understanding of the property’s condition, which can lead to smoother and more efficient transactions.
Frequently Asked Questions
Why is it essential for the buyer to attend the home inspection?
Attending the home inspection lets the buyer see the property’s condition firsthand and ask the inspector questions directly. This involvement is crucial for understanding any issues and planning future maintenance.
Can the seller refuse to allow the buyer to attend the inspection?
While uncommon, sellers can stipulate terms regarding who can attend the inspection. However, most sellers are cooperative and understand the importance of the buyer’s presence. It’s always best to discuss attendance expectations with your real estate agent beforehand.
What should I bring to the home inspection?
Buyers should bring a notebook, a camera (or smartphone), and a copy of the property listing. It’s also helpful to have a list of any specific concerns or questions about the property to discuss with the inspector.
Conclusion
Knowing who attends a home inspection in California is essential for a successful property transaction. The presence of the right people ensures a thorough evaluation, clear communication, and informed decision-making. Whether you’re buying, selling, or just planning for the future, understanding the roles and importance of each attendee can make the process smoother and more efficient.
Ready to schedule your inspection? Contact Signature Home Inspection today for a professional and comprehensive evaluation. Our expert inspectors ensure you have all the information you need to make confident decisions about your property.